What does Swiss Cheese, Safety and Construction have in common?
December 7, 2021
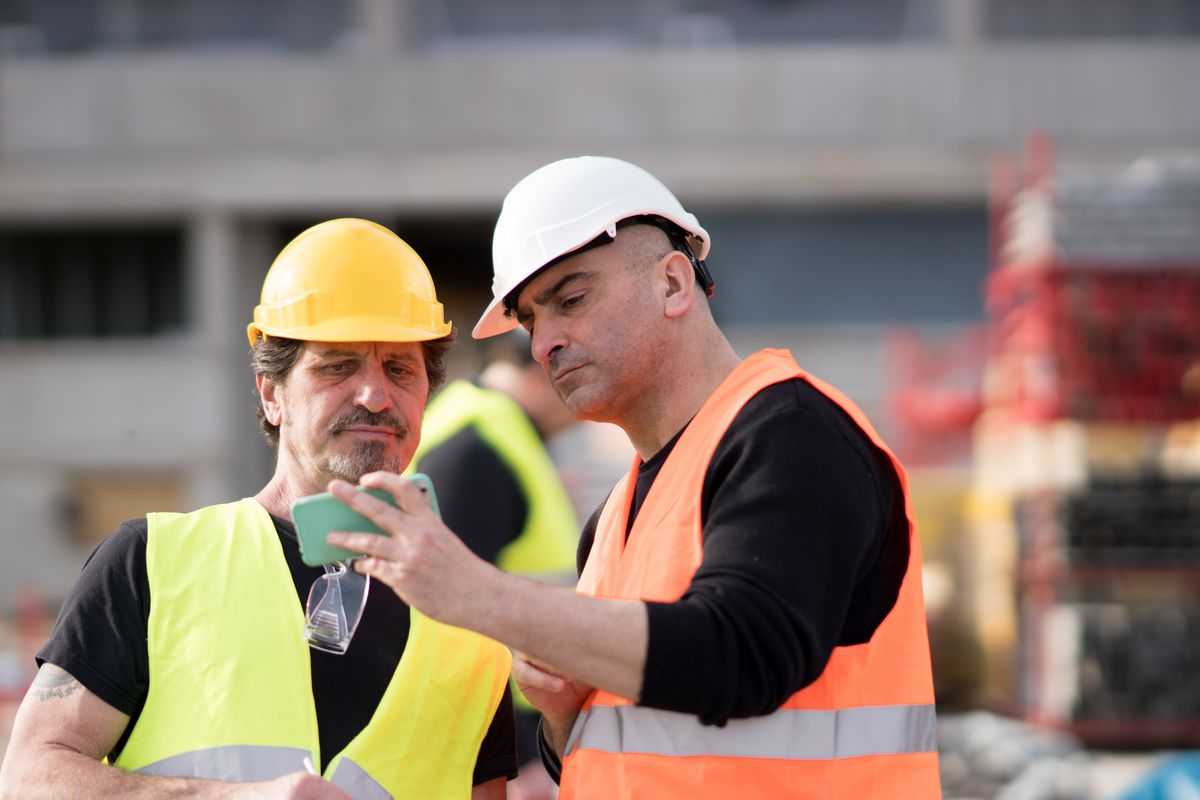
On a construction site, safety is never ‘done’. The risks on a site change by the millisecond - new hazards appear in an instant, and the people on-site change daily.
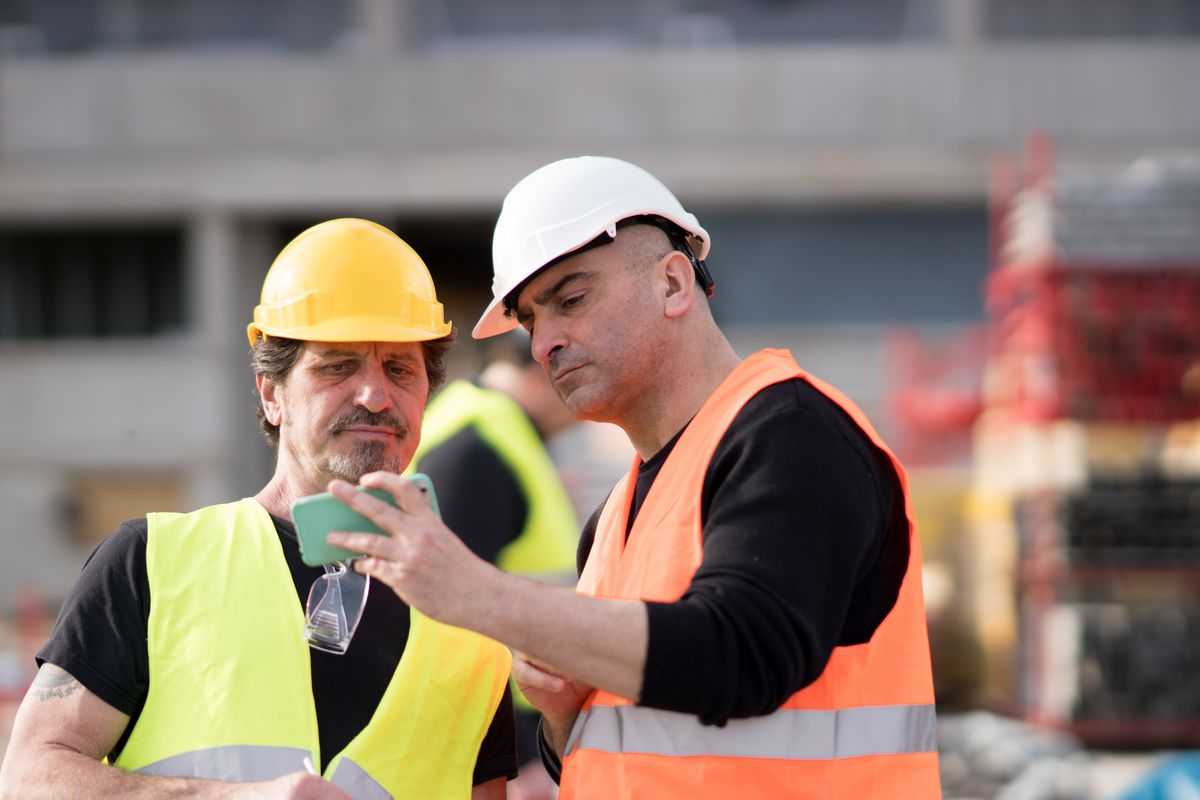
A big line of defence against injuries and incidents is the use of controls, from the top of the hierarchy to the bottom.
Above all else, we rely on communication to keep each other safe. After all, controls don’t work without being communicated. The communication could be anything from a formal process (like a Site Induction), to an announcement at a Toolbox Talk or a simple conversation between stakeholders.
By using controls, effective communication and continuous improvement, there has been a 70% reduction in safety incidents in the 33 years between 1974 and 2007 (source).
So why do we still have safety incidents? Why wasn’t the reduction 80%? Or 95%?
How incidents can still happen
One way we can analyse this problem is using the Swiss Cheese Model. The model states that accidents occur when multiple systems fail simultaneously.
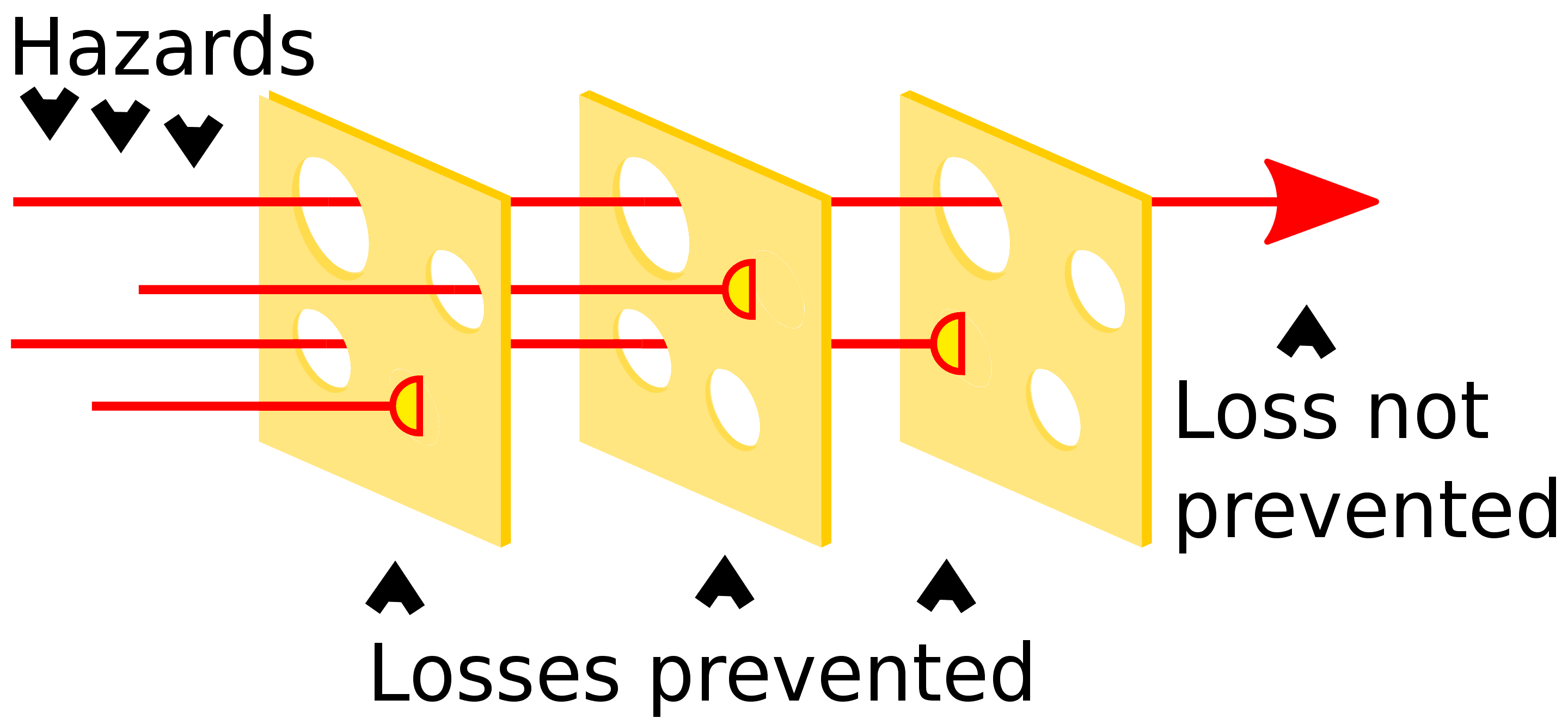
The Swiss Cheese Model
(By Ben Aveling - Own work, CC BY-SA 4.0, https://commons.wikimedia.org/w/index.php?curid=91881875)
Consider the scenario of Tim - an electrician who is a subcontractor of a subcontractor. He turns up on your site at 11am (after finishing up another job in the morning), well after the day’s first pre-starts were done.
He’s been inducted to the site, but that morning he missed a toolbox talk on working at heights. There was an injury the day before, and it was determined that a specific area of this fitout project has an elevated risk of injury. This risk was talked about extensively at the Toolbox Talk, and a memo was pinned up on the notice board.
Tim’s there to get on with the job, so after he’s inducted, he walks straight past the notice board. On top of not having been part of the Toolbox Talk, he’s missed the backup control of the printed sheet.
The holes on the slices of cheese (controls) lined up and the safety system failed. The electrician is still at risk as if neither of those systems existed in the first place.
Filling the gaps
How can we stop, or at least reduce the likelihood of this happening again? Generally, the response is to add to the systems of controls and communications.
Using the Swiss Cheese model, these responses seek to reduce the risk by:
- Adding more slices to the system,
- Reducing the sizes of the holes in each slice,
But the human reality of construction work tells us that it’s not so simple. Adding to systems doesn’t always make it better - it can make the system worse.
Making controls more complex (by adding slices or making the holes smaller) runs the risk of workers feeling that they’ve got extra roadblocks to getting their job done. The “new and improved” controls don’t get engagement from the workforce, which means the risk mitigation isn’t in place.
The intent behind the control doesn’t translate into reality. It could even have the unintended consequence of creating a new risk. If this happens, we’ve done no favours to the safety culture on site, and people are still able to fall through the cracks (or holes) in the way we work.
The bigger picture
Addressing a safety problem requires us to look at the bigger picture - we start at the point of failure and zoom out to get the full context of what happened, what we want to achieve and the human behaviours at play.
As this common scenario shows, having a process in place doesn’t always get the job done because of the unexpected variables of reality.
At the end of the day, what Tim needed was communication. It could have come in a formal process or a heads-up from someone on site. The message being heard is important - not how it is delivered.
We’re unlikely to find a single perfect solution to this scenario. A more pragmatic goal is to ask ourselves, “are we using all of the methods and tools at our disposal?”.
In the scenario above, a tool left on the table was technology.
On a construction site, everyone carries a device purpose-built for communication - their mobile phone. What if Tim’s phone buzzed him as he approached the site alerting him to yesterday’s injury? He could ask the Supervisor about it during his Induction and be fully informed of the situation.
.jpeg)
This simple slice of cheese doesn’t fundamentally change the system or substitute for other controls, but it did catch what the others missed by adding the extra layer.
This is a solution known as Connected Worker Technology - practical technology that helps people get their job done quickly and safely. Systems like SignOnSite let managers and supervisors communicate with workers, and run workflows with them in real-time. In Australia, 27% of the construction industry is using Connected Worker technology to turn workers into active participants in site safety.
The brand of the tools used doesn’t matter - the impact it has on your workforce does. Great safety technology should feel as natural as any tool on site, and be a partner to the systems you already have. When it comes to your obligation to consult, cooperate and coordinate with workers on site, good technology should be another helpful ‘slice of cheese’ that has your back.